I. Complexity of Functional Requirements: The Dilemma of Balancing Multiple Performances
Doors and windows serve as the interface between buildings and the external environment. They must simultaneously meet requirements for lighting, ventilation, sound insulation, security, and waterproofing—functions that often conflict with one another. Design must achieve a precise balance on the technical level.
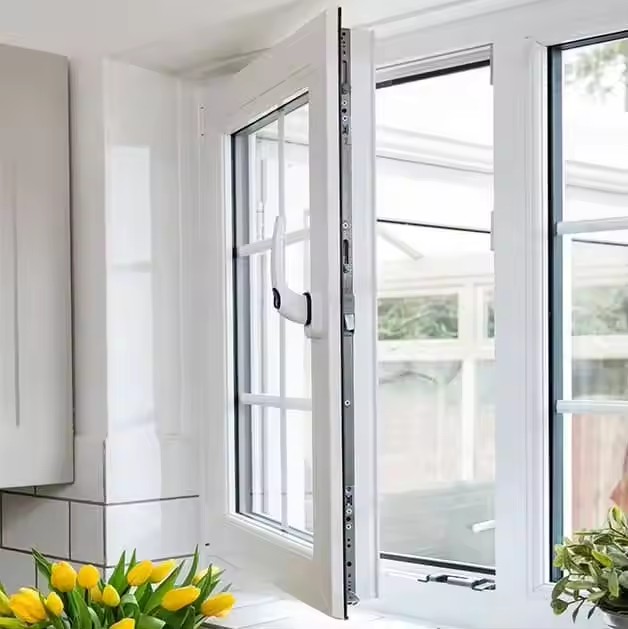
- Dynamic Balance Between Daylighting and Shading
Challenge: Large glass areas improve daylighting but also increase solar heat gain in summer, adding to the indoor cooling load. For instance, in southern regions, solar radiation intensity at noon can reach 800W/m². Standard single-pane glass has a shading coefficient (SC) of about 0.9, meaning 90% of the heat enters the room.
Solution: Use Low-E glass (emissivity ≤ 0.15), shading louvers, or smart glass (e.g., electrochromic glass). However, these technologies increase costs, and louver angles must be optimized through simulation to balance shading and lighting efficiency. - Conflict Between Ventilation Efficiency and Airflow Control
Challenge: Natural ventilation requires sufficient airflow (e.g., ≥3 air changes/hour in residential buildings), but open windows can let in noise, dust, or rain. For example, cross-ventilation in high-rise apartments can produce wind speeds up to 5 m/s, causing indoor airflow turbulence and discomfort.
Solution: Use adjustable ventilators (e.g., micro-ventilation systems with filters) or incorporate air deflectors into the window design. However, the angle of deflectors must be verified via Computational Fluid Dynamics (CFD) simulation to avoid excessive resistance that reduces ventilation efficiency. - Multilayered Challenges of Acoustic Insulation
Challenge: Different noise sources require different insulation solutions (e.g., traffic noise is mostly low-frequency, while industrial noise includes high-frequency components). A residence near a busy street may need to block over 50 dB of noise, while standard aluminum windows only offer 25–30 dB.
Solution: Use multi-layer insulated glass (e.g., 5+12A+5+12A+5) with PVB interlayers to absorb high-frequency noise. The window frame and wall joints must use multiple EPDM seals. The compression range and aging cycle of these seals (typically 5–8 years) should be accounted for in the design for maintenance purposes. - Conflict Between Anti-theft Security and Ease of Use
Challenge: Anti-theft windows and doors must resist prying and impact (e.g., European RC2 standard requires 15 minutes of forced-entry resistance). However, strong materials like stainless steel lock points increase opening resistance, affecting daily usability.
Solution: Use concealed hinges and multi-point locking systems (e.g., 3- or 5-point locks), along with smart locks (fingerprint, keypad, or remote access). But electronic components must meet waterproof standards (≥IP54) and battery life requirements (≥12 months), which must be considered during structural design.
II. Technical Bottlenecks in Material Selection: A Game of Performance, Cost, and Process
The physical properties of window and door materials directly determine the design ceiling, and their weaknesses must be compensated for through technical innovation.
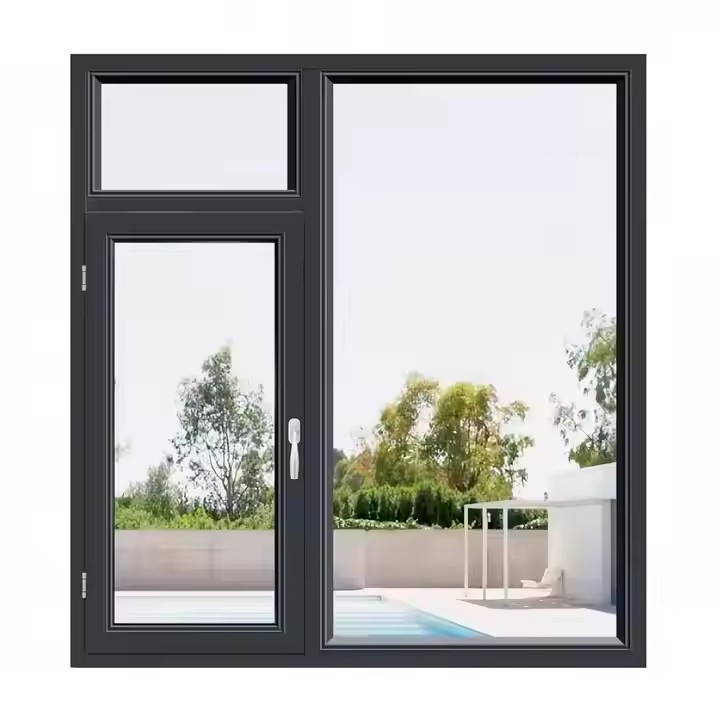
- Thermal Insulation Limitations of Metal Materials
Aluminum Profiles: High thermal conductivity (200 W/m·K); traditional aluminum windows may have heat transfer coefficients (K-values) up to 5.0 W/m²·K, far above energy-saving standards.
Solution: Use “thermal break” aluminum profiles with PA66 insulation strips (thermal conductivity ≈ 0.3 W/m·K) to form multiple insulation chambers, reducing K-values to below 2.5 W/m²·K. However, insulation strip width (typically ≥20 mm) limits profile design and may impact slim aesthetic appeal.
Steel: High strength (≥345 MPa tensile strength) but poor corrosion resistance, requiring hot-dip galvanizing (zinc layer ≥85μm). Difficult to process—minimum bending radius is 3× wall thickness, limiting complex shapes. - Natural Defects and Modification of Wood
Challenge: Solid wood is prone to deformation due to humidity (moisture content must be kept between 8%–12%) and has poor weather resistance. For example, red pine has a swelling rate of up to 8%, so a 1.5-meter-wide window could deform by 12 mm in environments with 20°C temperature swings and 40% humidity changes.
Solution: Use engineered wood (finger-jointed) to reduce internal stress or apply aluminum cladding (aluminum-clad wood windows). However, the sealant between aluminum and wood must withstand temperature cycling (-30°C to 70°C) to prevent cracking and leakage. - Strength Limitations and Optimization of Plastic Profiles
PVC Profiles: Low cost (about 1/3 of aluminum), but low tensile strength (only ~50 MPa). Large windows (e.g., 2.4-meter-tall floor-to-ceiling windows) require internal steel reinforcements (≥1.5 mm wall thickness). Welding also demands high precision (welding temp: 240±5°C), or weld strength may fall short (standard ≥3000 N).
New Materials: Fiber-reinforced plastic (FRP) offers high tensile strength (≥300 MPa), but mold costs are high (≥500,000 RMB per set). Its thermal expansion coefficient (25×10⁻⁶/°C) is significantly different from glass (9×10⁻⁶/°C), increasing the risk of seal failure.
III. Multi-Dimensional Structural Design Conflicts: Technical Challenges from Opening Modes to Wind Pressure Resistance
The structural configuration of doors and windows directly influences performance limits. The design must find the optimal solution among mechanical strength, sealing performance, and durability.