- Material Selection
1.1 Panel Materials
Use of Environmentally Friendly Panels: Choose artificial boards that comply with national environmental standards, such as E0 or E1 grade particleboard, fiberboard, or plywood. E0 grade panels have a lower formaldehyde emission, with a release limit of 0.05 mg/m³, significantly lower than the E1 grade, which has a limit of 0.125 mg/m³. These materials are produced using low-formaldehyde or formaldehyde-free adhesives, reducing the release of harmful gases from the source. Using environmentally friendly materials can help reduce the costs of high-priced materials. As more people prioritize environmental protection, sustainable products have become increasingly popular. Therefore, when designing products, it is important to focus on environmental friendliness.

Eco-Frie
ndly Adhesives: During the production of casement doors, when assembling panels or attaching decorative materials, formaldehyde-free or low-formaldehyde adhesives should be used. For instance, soy protein adhesives, made from soybean protein, are natural and environmentally friendly. They offer strong bonding performance and have very low formaldehyde emissions, meeting high environmental standards. The use of these eco-friendly adhesives is becoming increasingly popular in the market, as people are more focused on sustainability and prefer products with environmentally friendly processes.
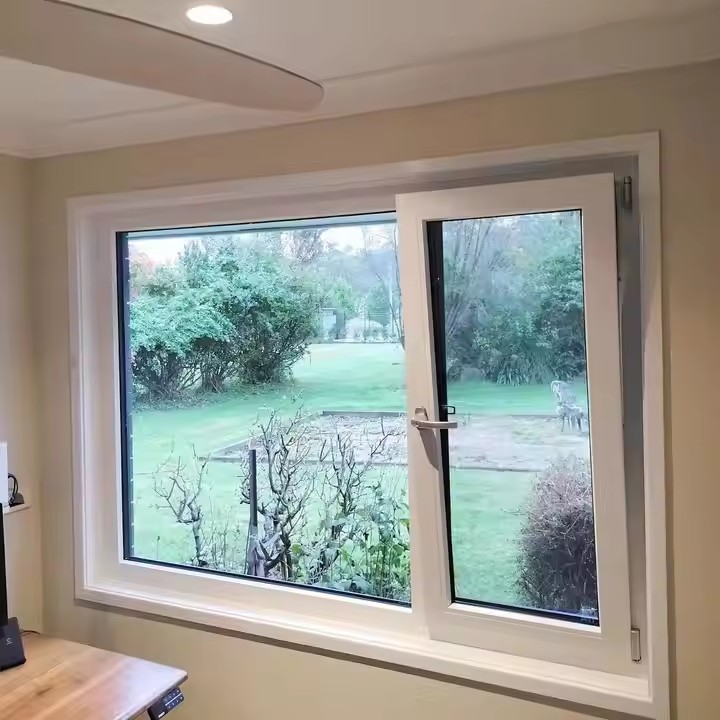
- Production Process Optimization
2.1 Precise Processing to Reduce Waste
Using high-precision cutting and processing equipment can ensure that materials are processed according to the exact design specifications. For example, CNC cutting machines can control the cutting error to a very small range, which helps to minimize material waste. By reducing waste, not only are production costs lowered, but the environmental impact of solid waste is also reduced. The glass cutting process must be precise to minimize material waste. Leftover glass pieces and corner cuts can also be reused to prevent waste. Similarly, window and door accessories should be precisely measured and cut to save costs.
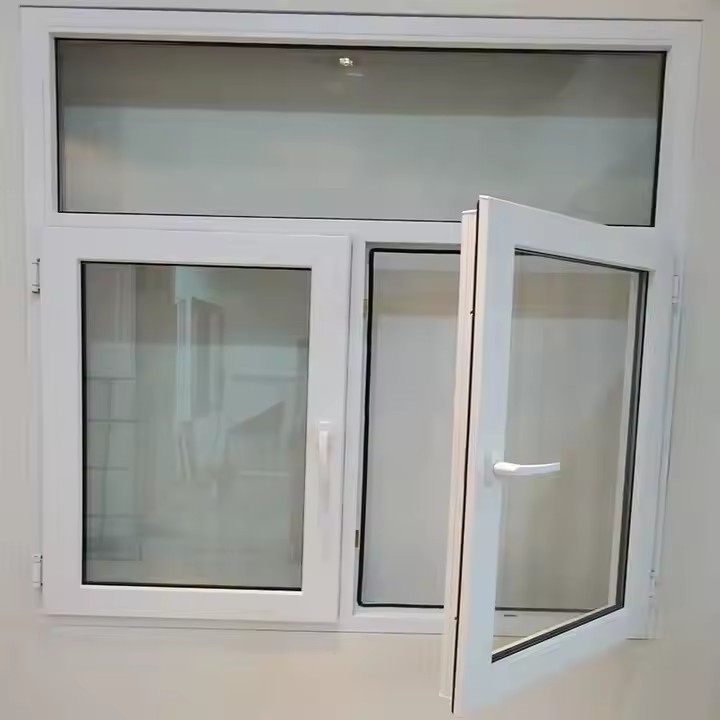
2.2 Energy-Saving Production Measures
Energy-Efficient Equipment: Energy-saving retrofits can be implemented on production equipment. For example, variable frequency drives can be installed on machines to adjust the motor speed according to the actual production needs, reducing energy consumption. In processes like drying and coating of casement doors, energy-efficient drying equipment and spray booths can be used, optimizing heating and ventilation systems to effectively utilize energy and minimize waste. By investing in energy-efficient equipment, the overall production cost is reduced, which translates to less energy and labor costs.
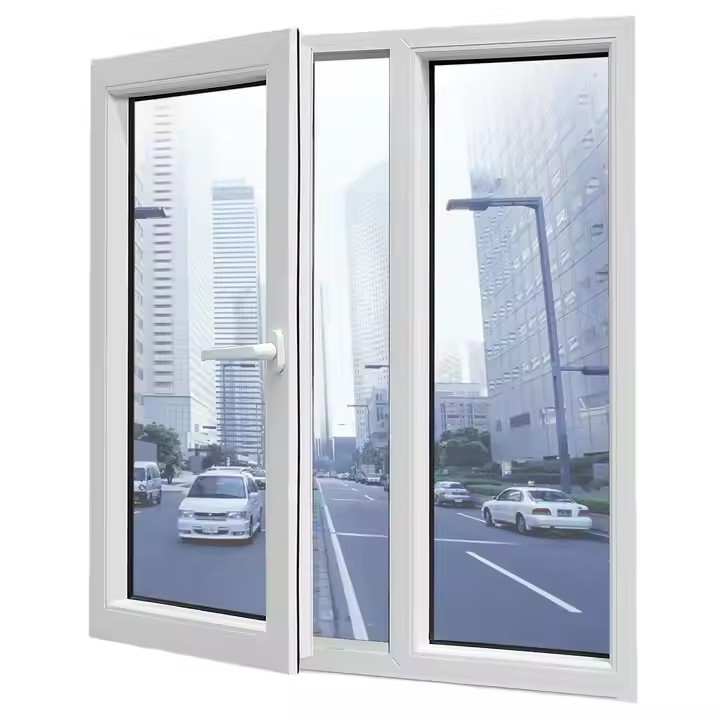
Energy Management System: Establishing a comprehensive energy management system allows for real-time monitoring of energy consumption across all production stages. By analyzing energy data, areas where energy is being wasted can be identified and optimized. For instance, production schedules can be adjusted to avoid unnecessary equipment operation during idle periods, further reducing energy consumption. Energy-saving measures should be continuously monitored, with equipment faults detected and repaired promptly to prevent additional energy loss.
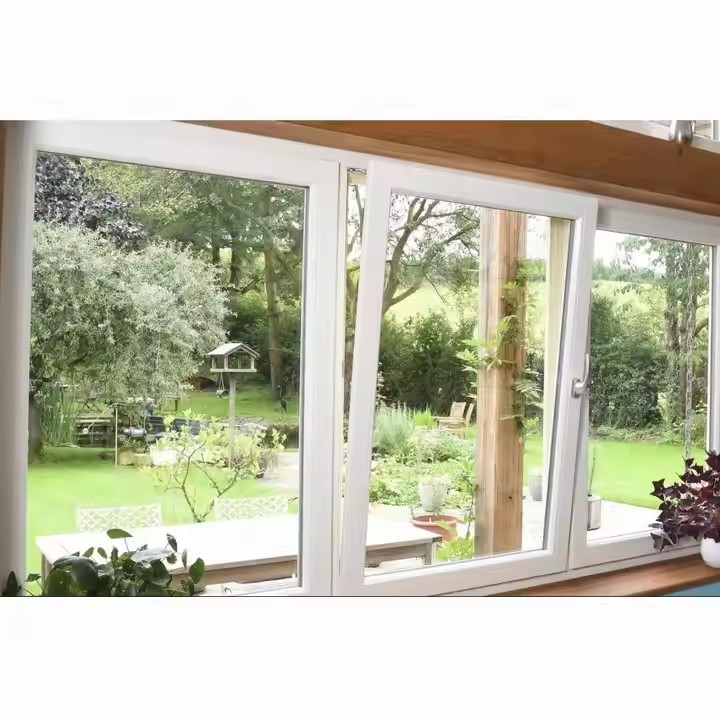
3、Quality Control and Testing
3.1 Raw Material Testing
Each batch of raw materials entering the factory should undergo strict environmental testing. For panels, in addition to checking their physical properties, the focus should be on formaldehyde emission levels and other environmental indicators. Scientific testing methods, such as climate box tests, can be used to simulate real-world environmental conditions and accurately measure formaldehyde and other harmful gas emissions from the panels. For coatings and adhesives, the composition lists and environmental certification documents should be examined, and samples should undergo testing to ensure they meet environmental standards.
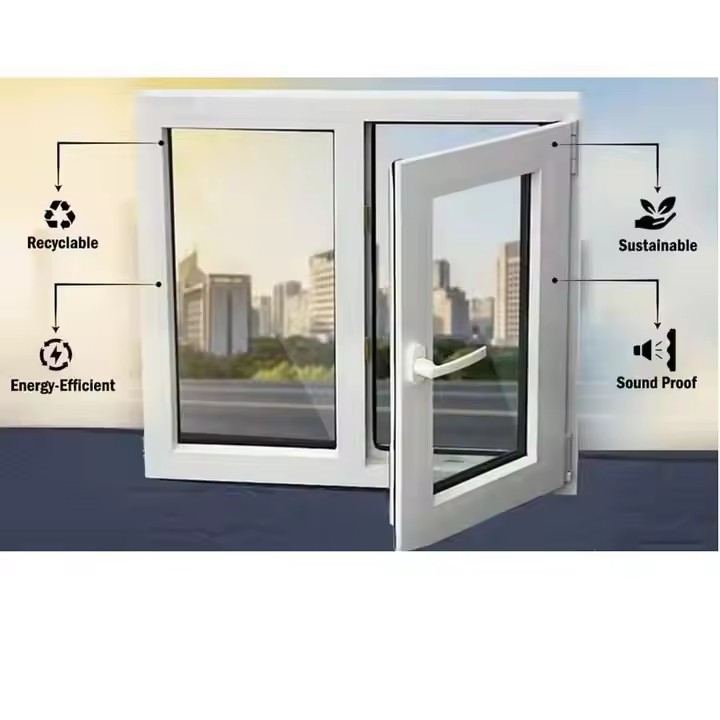
3.2 Finished Product Testing
Once the casement doors are produced, comprehensive environmental performance testing should be conducted. Tests may include indoor air quality testing, where the doors are placed in a simulated indoor environment to assess whether harmful gas emissions exceed safe levels. Additionally, the surface of the doors should be tested for harmful substance residues, such as heavy metals. Only products that pass strict environmental testing can be released to the market, ensuring they meet high environmental standards.
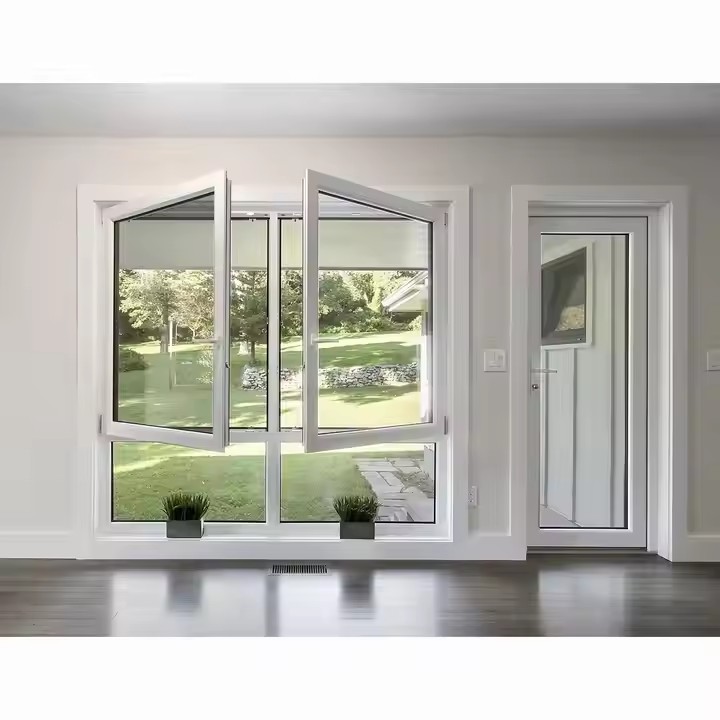
- Packaging and Transportation
4.1 Eco-Friendly Packaging Materials
Use recyclable and biodegradable packaging materials. For example, paper-based fillers can replace plastic foam, as paper fillers can be easily recycled after use. For outer packaging, cardboard boxes made from recyclable materials should be used, which are biodegradable and cause less long-term environmental pollution compared to plastic packaging.
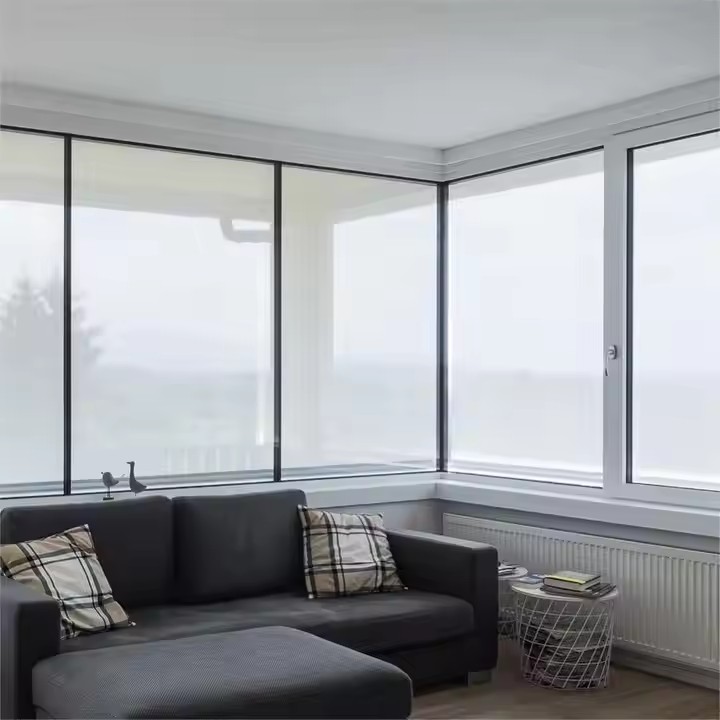
4.2 Efficient Transportation Planning
Optimize transportation routes and methods to reduce energy consumption and emissions during the transportation process. Logistics planning software can help identify the shortest and most efficient transportation routes. Additionally, transport vehicle loads should be optimized to improve transportation efficiency and reduce the carbon emissions per unit of product.