- Sealing Design
Door Gap Sealing Strips
Choosing high-quality sealing strips is key. For example, using EPDM (ethylene propylene diene monomer) rubber strips, which have good elasticity, aging resistance, and weather resistance. The shape of the sealing strips can be designed with multiple sealing lips, such as dual or triple lips. When the folding door is closed, these lips can effectively block the flow of air. For example, installing a sealing strip with dual lips at the door’s edge—the first lip blocks most of the wind, and the second lip acts as a backup, providing additional sealing during strong winds. High-quality sealing strips can protect the indoor environment better, preventing rainwater from seeping in during windy and rainy weather, and keeping dust or debris from blowing inside. In both windy and rainy conditions, the indoor environment can be better protected.
The installation method of the sealing strips is also crucial. The sealing strip should be tightly fitted to the door and door frame. A slot-based installation can be used, where the strip is embedded into a specially designed slot, making it less likely to shift. Additionally, the contact points between the sealing strip and the door or frame can be designed with a slight curvature, so the sealing strip compresses better when the door closes, enhancing the sealing effect. The installation must match the specific slots of the folding door, as each door has different slot configurations. Sealing strips can increase the door’s overall airtightness, preventing indoor temperature loss in winter and keeping cool air inside during summer, thus saving energy.
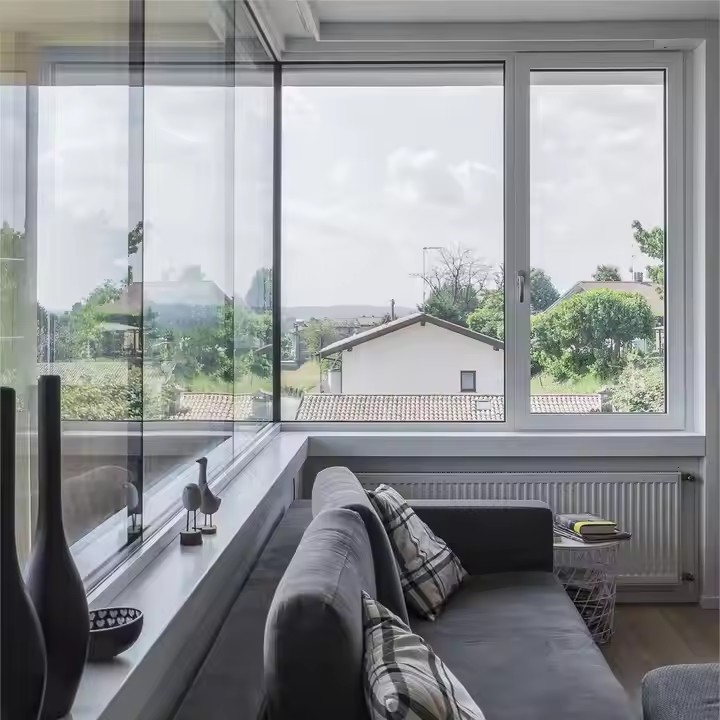
Sealing Between the Door Frame and Wall
Foam sealant can be used to fill the gap between the door frame and the wall. After curing, the foam sealant forms a continuous, elastic sealing layer, filling small gaps and preventing wind from entering. For example, when installing the folding door frame, foam sealant should be evenly applied along the gap between the frame and wall. After it expands and solidifies, it provides good sealing performance. Additionally, a decorative sealing strip can be added over the foam sealant to enhance both the sealing effect and the aesthetics.
- Hardware and Structural Design
Hinge and Track Design
For folding door hinges, high-strength and precision products should be selected. High-precision hinges ensure that the door closes tightly against the frame. For instance, heavy-duty stainless steel hinges can withstand strong wind without deformation. The hinge’s central axis can be designed with a damping device, which helps the door close slowly and tightly, ensuring that the sealing strip works effectively.
Track design must consider wind resistance and stability. The width and depth of the track should match the folding door’s rollers. The track can also be equipped with windproof brushes along its sides. When the door closes, the windproof brush contacts the rollers, blocking wind from the sides. Additionally, materials like aluminum alloy, which have higher strength, can be used to ensure the track does not deform under long-term use or wind pressure.
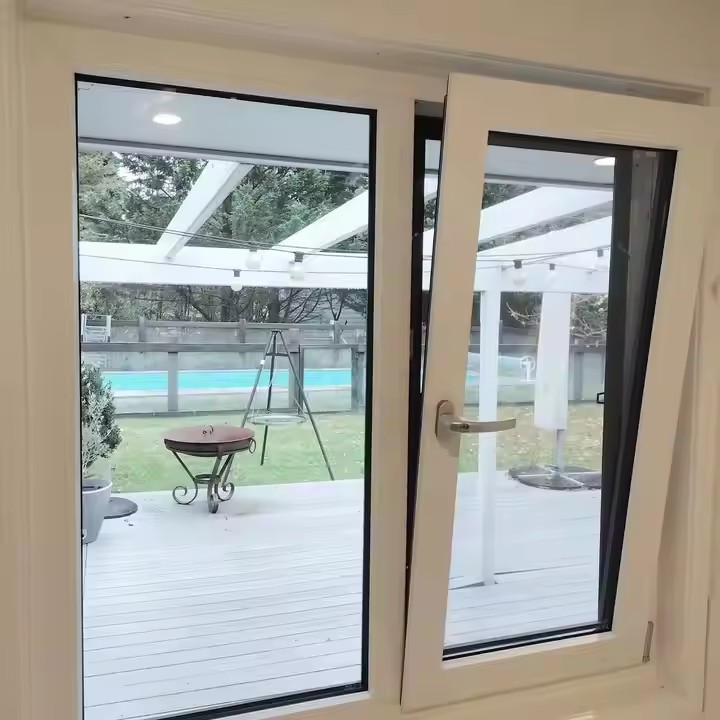
Reinforcing the Door’s Structural Strength
Reinforcement ribs can be added inside the folding door panels. These ribs can be made of metal materials such as aluminum alloy or steel and distributed logically based on the door’s size and weight. For larger folding doors, horizontal and vertical reinforcement ribs can be installed at the top, bottom, and center of the panel to increase the overall strength, making it less likely to deform under wind pressure. The door frame should preferably be made from strong aluminum alloy, ensuring it doesn’t bend in harsh weather conditions and maintains its original shape.
The choice of material for the door panel also affects wind resistance. Using double-glazed or insulated glass as part of the door panel can provide thermal and sound insulation and improve stability. When selecting glass, consider its thickness and quality. Generally, thicker glass can resist wind pressure better. For example, 6mm – 8mm thick double-glazed glass can significantly improve wind resistance. The material should also be chosen to be more wind-resistant, increasing durability and service life.
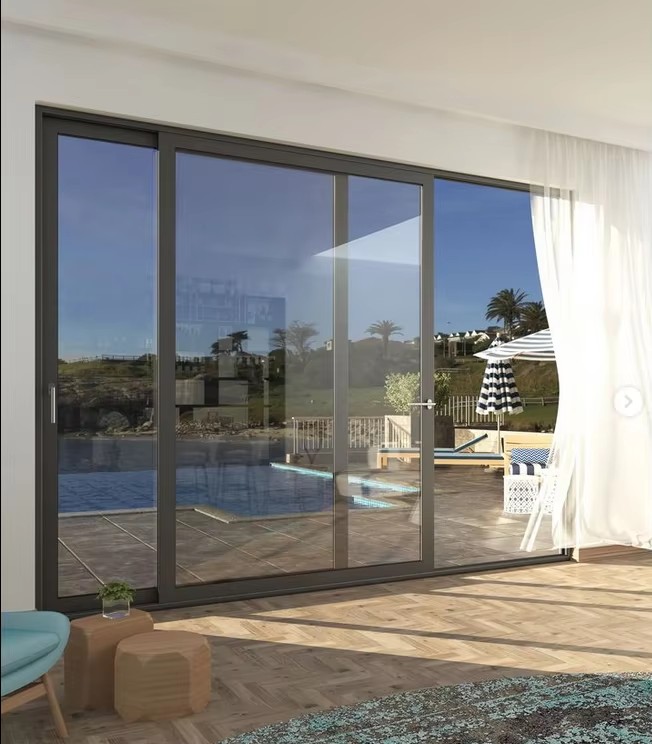
Installation and Debugging
Precise Installation
Ensuring the folding door is installed level and vertical is crucial. If the door is not aligned properly, uneven gaps can form, affecting wind resistance. Use professional tools such as a level and plumb line to measure and adjust the door frame during installation. For instance, first use the level to check if the bottom of the door frame is level, then use the plumb line to check if the sides are vertical, adjusting the position accordingly.
Each component of the folding door, such as hinges and tracks, should be installed according to the manufacturer’s instructions. Pay attention to the precision of the parts’ fit to ensure the door folds and closes smoothly, with a tight seal when closed. Installation guidelines can be printed on the outer packaging of the door to help workers reduce installation difficulties.
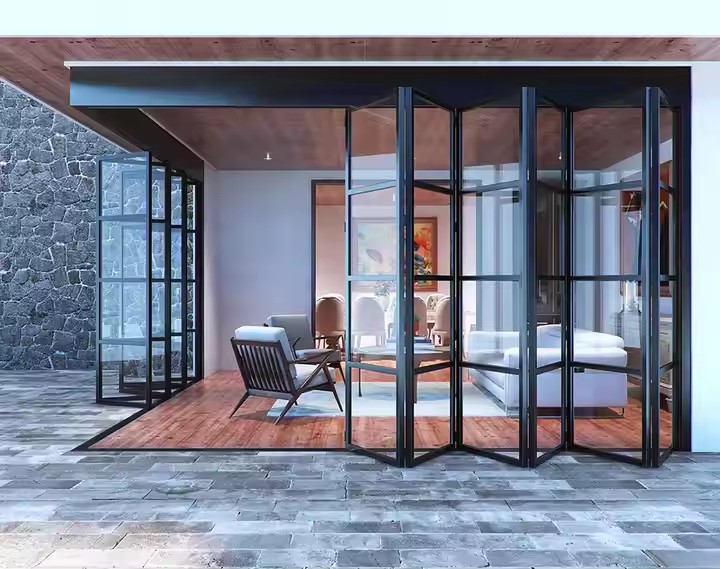
Debugging and Inspection
After installation, the folding door should be debugged. Check if the door opens and closes smoothly and if there are any gaps when closed. One method is to insert an A4 sheet into the door gap; if the paper is difficult to pull out, it indicates a good seal. If gaps or poor sealing are found, check if the sealing strips are correctly installed, and adjust the hinges and tracks as needed. Wind resistance can be tested by simulating various wind speeds, such as using an industrial fan to blow wind from different angles, observing the door’s sealing and stability. After installation, a review should be conducted to identify areas for improvement, optimize processes, and save materials, thus enhancing installation efficiency and resource conservation.
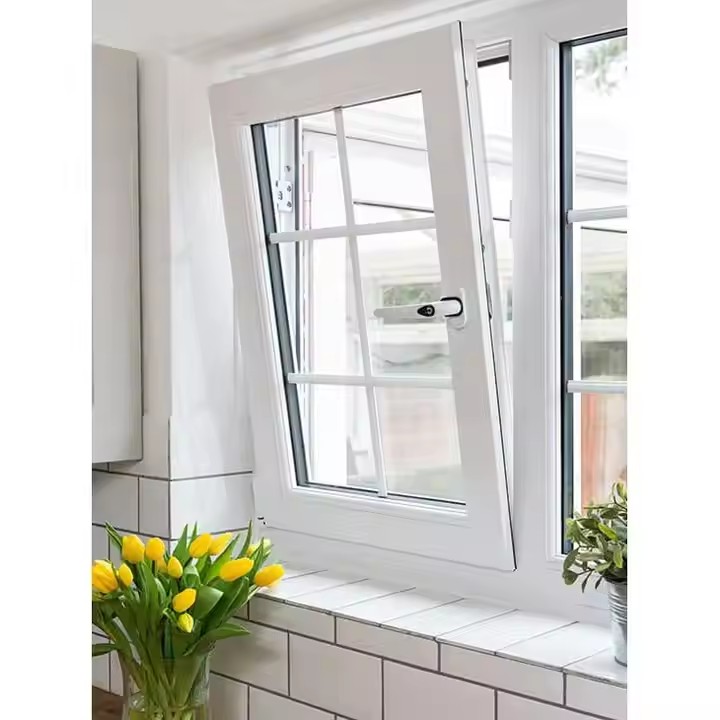