I. Material Selection
Frame Materials
Metallic Materials: For the frames of folding doors, manufacturers can choose high-strength aluminum alloys. Aluminum alloys are characterized by being lightweight and having high strength. Their alloying components (such as the addition of elements like magnesium and silicon) can further enhance strength through processes like heat treatment. For example, 6061 aluminum alloy, after undergoing T6 heat treatment, can have a yield strength of around 276 MPa and is capable of withstanding relatively large external forces. Moreover, aluminum alloys are corrosion-resistant and suitable for various environments, including damp bathrooms and outdoor balconies. Metallic materials have good quality advantages. They are lightweight, so they have high adaptability to installation scenarios. In addition, metallic materials have relatively good compressive resistance. Even after installing glass on the door frame, there is no need to worry that the weight of the glass will collapse the door frame.
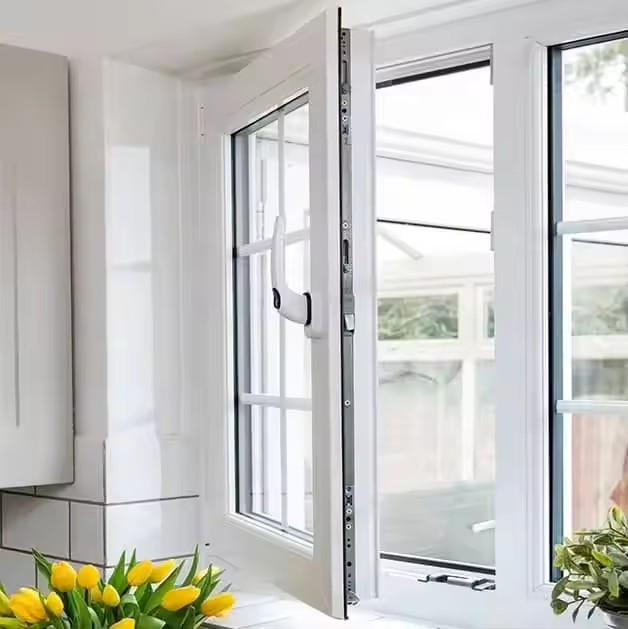
Composite Materials: There are also some new composite materials, such as fiber-reinforced plastics (FRP). It consists of fiber materials (such as glass fiber and carbon fiber) and a plastic matrix (such as epoxy resin). Carbon fiber-reinforced plastics can have a tensile strength reaching 3000 – 7000 MPa. This material has a high specific strength (the ratio of strength to density), which can reduce the weight of the folding door while providing excellent structural strength. Composite materials are relatively new and innovative materials with a relatively high cost-performance ratio. If your financial situation is not particularly good, you can purchase this kind of composite material.
Door Panel Materials
Glass Materials: If the folding door uses glass door panels, manufacturers can choose tempered glass. The strength of tempered glass is 3 – 5 times that of ordinary glass, and its flexural strength can reach about 125 MPa. It is made through a process of heating to near the softening point and then rapid cooling, forming compressive stress on the glass surface and tensile stress inside. When subjected to external forces, the stress distribution can effectively resist damage. For places with higher safety requirements, laminated glass can also be used. It has a polyvinyl butyral (PVB) film sandwiched between two or more pieces of glass. Even if the glass breaks, the fragments will be adhered to by the film and will not scatter, while also increasing the overall impact resistance.
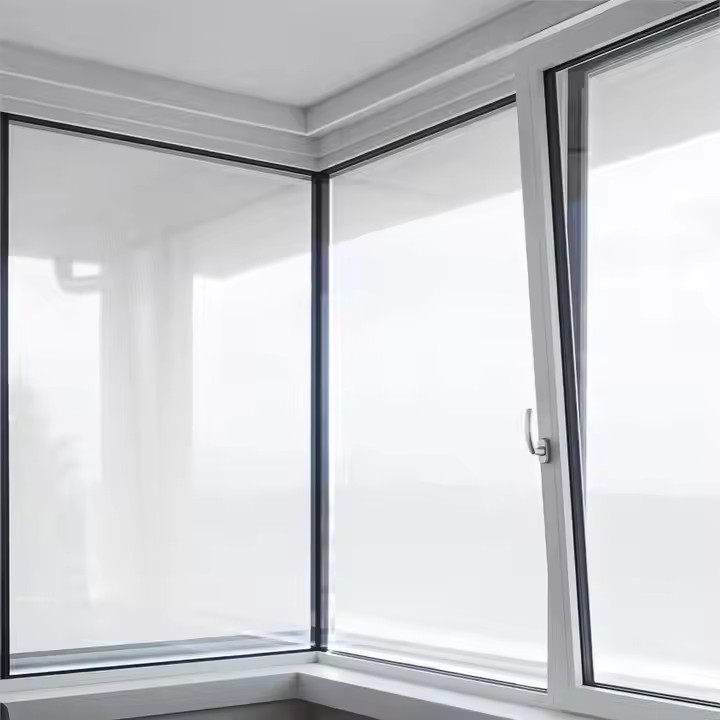
Board Materials: For wooden or plastic door panels, choosing multi-layer board or honeycomb board structures can improve strength. A multi-layer board is formed by gluing multiple thin wooden boards together, and the grain directions of adjacent layers are perpendicular to each other, which can effectively disperse stress and improve the flexural and anti-twisting abilities of the door panel. A honeycomb board has a honeycomb-shaped core material (such as paper honeycomb or aluminum honeycomb) in the middle and panels on the upper and lower sides. This type of board is lightweight but has relatively high compressive and flexural strengths because the honeycomb structure can well disperse external forces.
II. Design and Structural Optimization
Design of Connection Structures
The connection parts of folding doors are crucial. Manufacturers can use sturdy hinges or butt hinges. For example, heavy-duty hinges made of stainless steel have their rotating shafts precisely processed and can bear relatively large weights and frequent opening and closing actions. The thickness and width of the hinges also affect their load-bearing capacity. Thicker and wider hinges usually can provide better support. For large folding doors, multiple hinges can be installed in a distributed manner to evenly share the weight of the door. High-quality hardware should be used for the connection parts of folding doors. Since accessories for doors and windows, such as hinges and screws, are frequently used, only high-quality screws can have a longer service life.
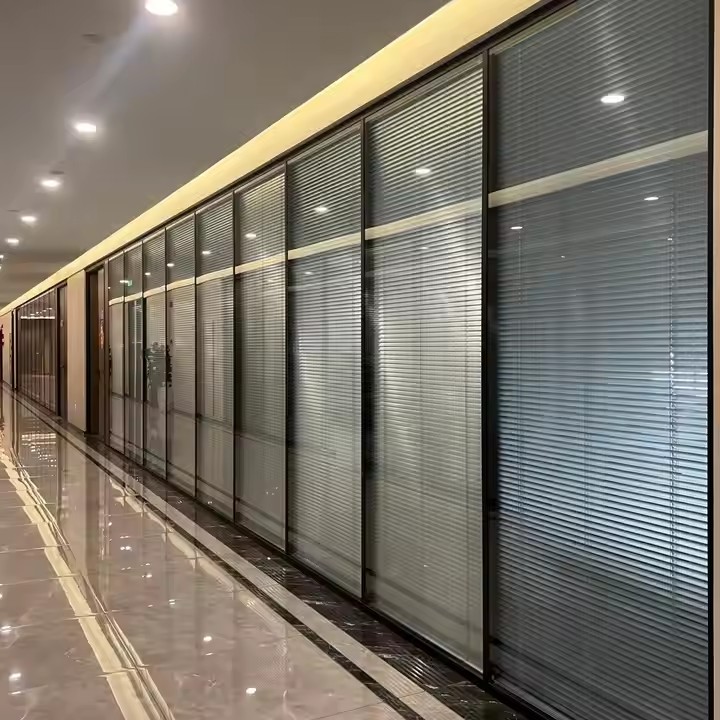
In terms of track design, high-strength aluminum alloy tracks or stainless steel tracks can be adopted. The shape and size of the tracks should match those of the pulleys, and they should have sufficient depth and width to ensure the stable operation of the pulleys within the tracks. The installation of the tracks should be firm. Manufacturers can fix the tracks on the wall or door frame by increasing the installation points, using expansion bolts and other means to prevent the tracks from loosening, thus ensuring the stability of the folding doors during the opening and closing process.
2、Reinforcement Structure Design
Reinforcing ribs can be added inside the frames of folding doors. For metal frames, metal reinforcing ribs can be installed through welding or riveting. For example, adding angle steel or channel steel as reinforcing ribs at the four corners and the middle of the long sides of the door frame can effectively improve the flexural and anti-twisting abilities of the frame. For wooden frames, wooden mortise and tenon structural reinforcements can be adopted, or metal connectors (such as corner brackets) can be used to enhance the strength of the joint parts.
For door panels, if they are relatively large-sized glass door panels, metal frames can be installed along the edges of the glass for reinforcement. The metal frames can be combined with the glass through adhesive bonding or mechanical fixation. This can not only protect the edges of the glass but also enhance the overall anti-deformation ability of the glass. For wooden or plastic door panels, a framed reinforcement structure can be set inside the door panels, just like installing wooden keels inside hollow door panels to improve the strength of the door panels.
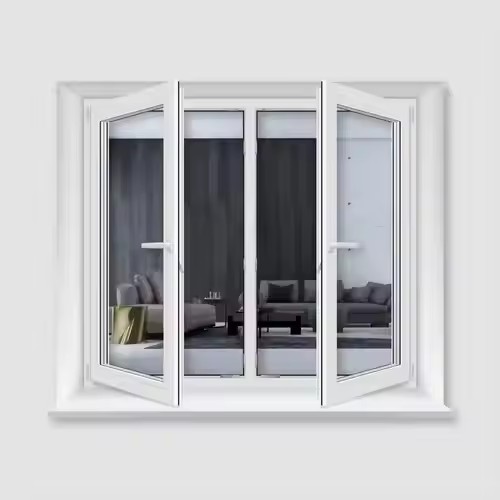
III. Manufacturing Process and Quality Control
- Control of Machining Precision
When manufacturing folding doors, manufacturers should strictly control the cutting precision of materials. For example, for the cutting of frame materials, the error should be controlled within a very small range to ensure that the splicing between various components is tight. If it is an aluminum alloy frame, the cut edges should be flat and smooth. Through high-precision cutting equipment (such as CNC sawing machines), the cutting error can be controlled within ±0.1 mm. In this way, when assembling, the connection parts of the frame can fit tightly, improving the overall structural strength.
For the processing of door panels, the control of surface flatness is also important. If it is a flat door panel, after being processed by equipment such as surface grinders, the deviation of surface flatness should be less than 0.2 mm. In this way, during the installation and use process, the fitting between door panels will be better, which can effectively prevent deformation and damage.
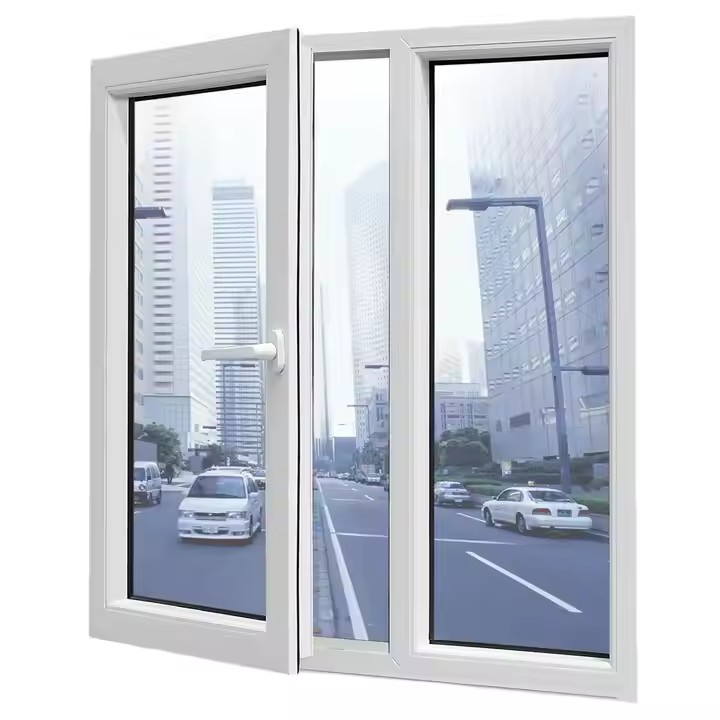