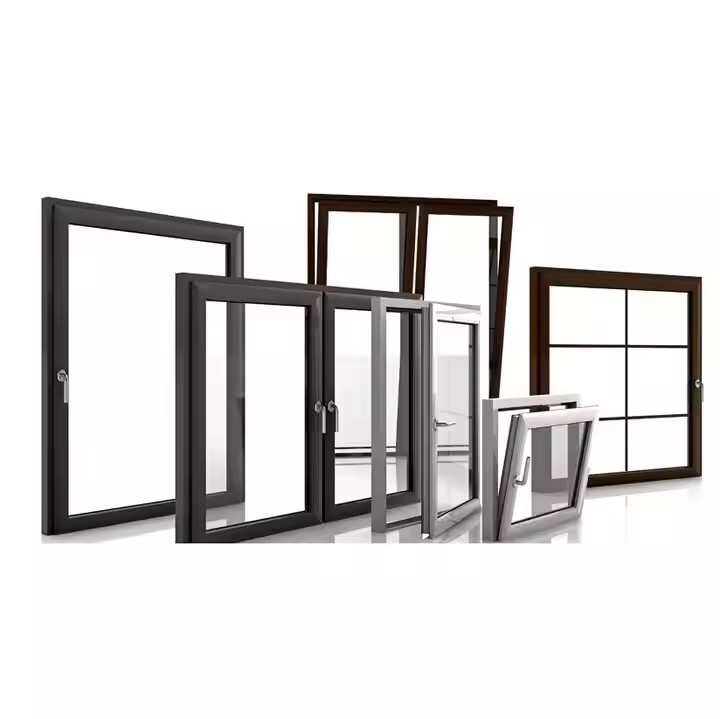
Design and R&D Stage
In the early stages of research and development, precise design specifications are crucial. Dimensions must be accurate, considering standard sizes for different building openings. The width, height, and dimensions of the sliding window frames must be strictly designed. Based on different design styles, the specifications for doors and windows will have varying heights and widths. Conduct market research, as the installation of casement windows varies by region. For instance, homes near the coast require windows with strong wind resistance, necessitating the development of wind-resistant window frames. For common residential sliding windows, the frame width typically ranges from 80 to 120 mm, and the height varies based on floor levels and room functions. It is essential to ensure that the window sashes slide smoothly within the frame and seal properly, with a typical gap of 3 to 5 mm between the sash and the frame. The structural design of the casement windows should be reasonable, utilizing a sturdy frame. For example, using a thermal break aluminum structure, where the insulating strip effectively blocks heat transfer while enhancing the strength of the frame. At stress points, such as the four corners of the frame, reasonable connection methods should be designed, typically using corner brackets connected and reinforced with adhesive, allowing the frame to withstand greater wind pressure and external forces. Meanwhile, optimizing material selection is crucial; for aluminum alloy sliding windows, high-quality aluminum alloy profiles should be chosen. The alloy composition must meet standards, such as 6063-T5 aluminum alloy, which has a balanced magnesium and silicon content, providing good strength and corrosion resistance. The wall thickness of the profiles should also meet requirements, with national standards stipulating that the wall thickness of the main load-bearing components should not be less than 1.4 mm to ensure the frame’s durability.
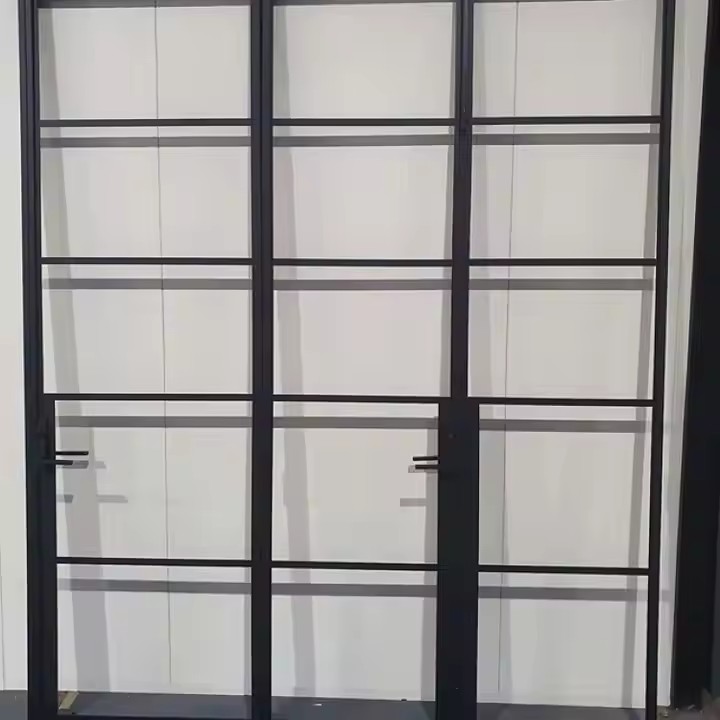
Raw Material Procurement Stage
To improve the quality of windows and doors in the factory, it is essential to carefully select suppliers and thoroughly evaluate the suppliers of frame profiles. This includes checking the suppliers’ production qualifications, equipment, and technological capabilities. For example, advanced extrusion equipment can produce aluminum alloy profiles with high dimensional accuracy and good surface quality. Assess the supplier’s quality control system to ensure they are certified under quality management systems like ISO 9001, which guarantees stable supply of products meeting quality requirements. Inspect the quality of material suppliers to ensure they meet national certification standards, eliminating suppliers with substandard materials that do not meet national standards. For glass and sealing strip suppliers, pay attention to their raw material sources and production processes. Glass suppliers should use high-quality raw materials like quartz sand, and their melting and forming processes must meet standards. The rubber mixing and extrusion processes of sealing strip suppliers should be advanced to ensure the quality of the strips. Raw materials should undergo rigorous inspection.
Inspect each batch of frame profiles. Check the appearance; the surface should be smooth, with uniform color and no visible scratches or dents. Measure the dimensions of the profiles, including wall thickness and cross-sectional size, to ensure compliance with design specifications. Perform sampling tests on the mechanical properties of the profiles, such as tensile strength and yield strength, using universal material testing machines. For glass, check its appearance for flatness, bubbles, and impurities. Conduct optical performance tests to ensure transparency meets design requirements. For sealing strips, check physical properties such as elasticity and hardness using hardness testers and tensile testing machines, and evaluate their aging resistance through accelerated aging tests.
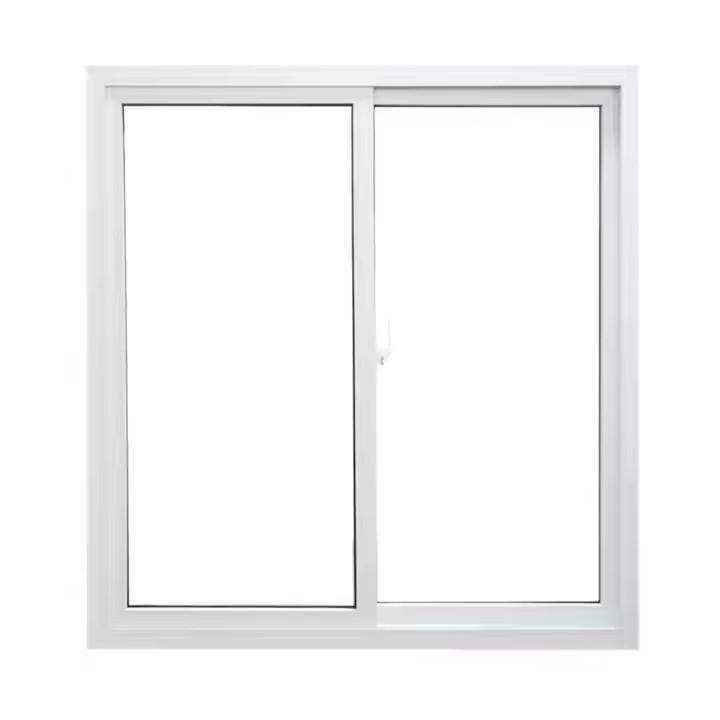
Production Processing Stage
To enhance the quality of window production in the factory, focus on updating and maintaining production equipment. The factory should be equipped with advanced production machinery. For frame processing, high-precision cutting equipment is essential for accurately cutting aluminum alloy profiles to a precision of ±0.5 mm. Use CNC machining centers for drilling and milling the frames to ensure processing precision and consistency. Regular maintenance of production equipment is necessary. Replace easily worn parts like cutting tools and molds in a timely manner; for instance, cutting tools should be replaced according to their specified lifespan to maintain cutting precision. Clean and lubricate the equipment to ensure normal operation; for example, regularly clean and lubricate the guide rails of machining centers to prevent precision loss due to dust and wear.
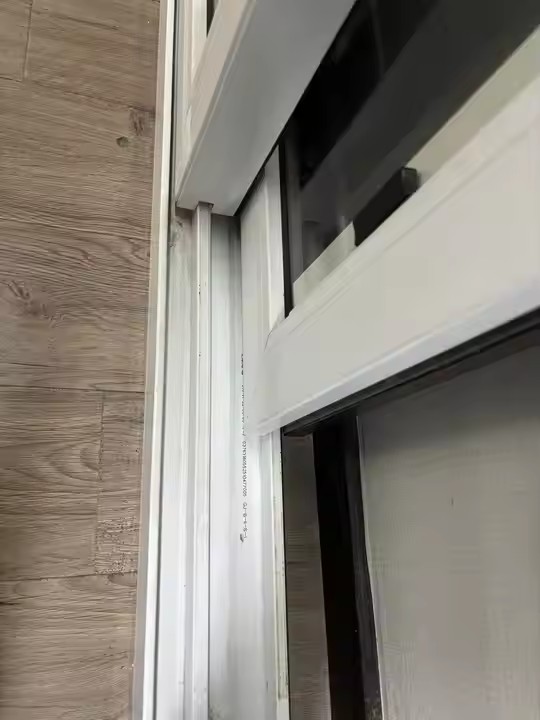
Production Process Control
The window frame assembly process must be strictly controlled. During corner bracket connections, ensure a tight fit between the brackets and the internal cavities of the profiles, and that the injected sealant is complete and uniform. For instance, use specialized injection equipment to control the amount and speed of sealant injection to ensure corner connection strength. The installation process of the window sashes is equally important. When installing glass, appropriate sealing gaskets should be placed between the glass and the frame to ensure the glass is securely installed and sealed. When installing sealing strips, the strips must fit into their grooves without twisting or falling out, ensuring tight sealing at the strip joints, which can be further secured with specialized adhesives.
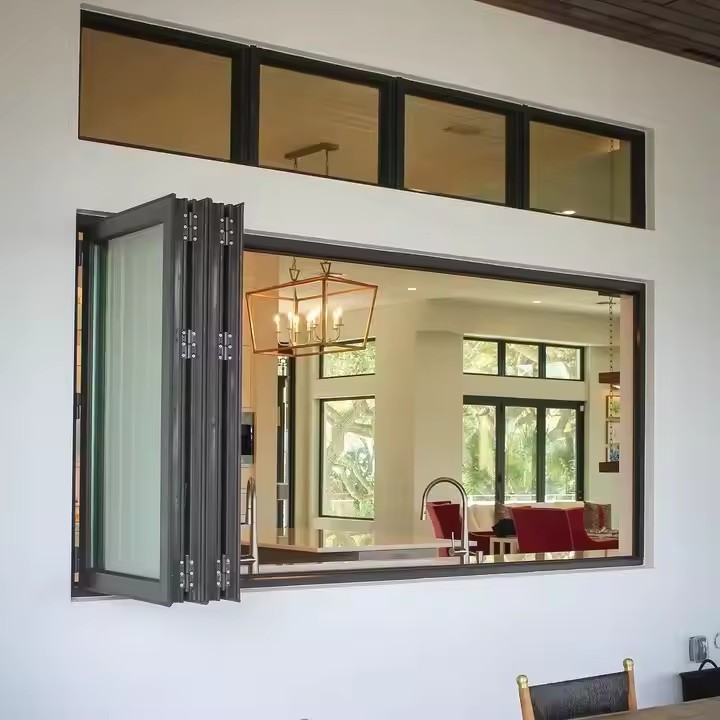