I. Production Planning Management
Order Analysis and Production Scheduling
According to customers’ requirements, the order quantity, carry out production, and clearly understand when the customers need the goods to be delivered. Also, you can know in advance about the transportation method, whether urgent delivery is required, etc. Because this is related to the integrity issue between the manufacturer and the customer, it is necessary to communicate clearly and timely during the interaction with the customer.
For example, if a customer needs 1,000 sets of doors and windows, the frame color is required to be white, and the delivery is required within 60 days, then production should be carried out according to these orders as required.
According to different procedures and the importance of different component productions, it is necessary to figure out which ones are important production processes. The important production components can be produced first, and the secondary production components can be produced later. Because production requires assembling parts and is carried out according to a certain order quantity, remember not to waste production resources.
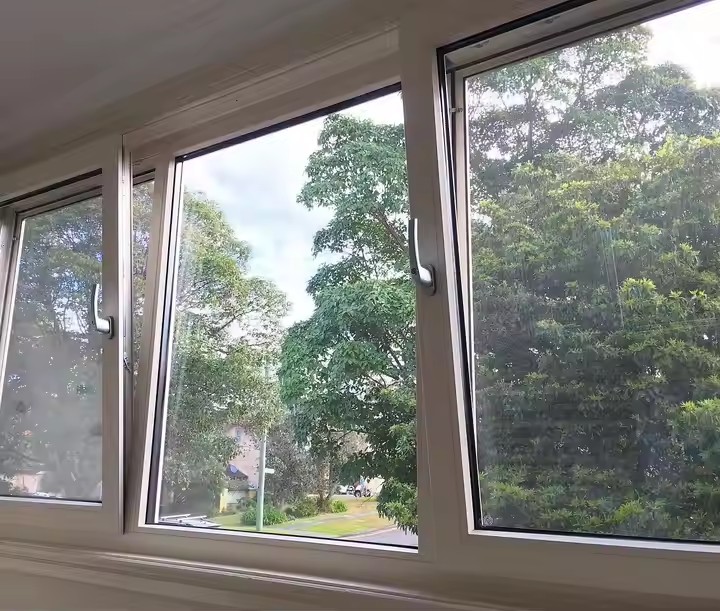
Progress Tracking and Adjustment
Establish a production progress tracking mechanism. Through methods such as daily production reports and on-site inspections, master the production progress in real time. For example, the production supervisor checks the production situation of each workshop every day and compares whether the actual progress matches the planned progress.
Control the daily production time and strictly control the use of time every day. The production process and production components of each day should be clear; otherwise, it is easy to make mistakes. Control the production timeline well.
If it is found that the progress is lagging behind, analyze the reasons in time, such as equipment failure, insufficient supply of raw materials, staff absenteeism, etc., and take corresponding measures to adjust. For example, increase overtime hours, temporarily allocate staff, or adjust the production process, etc. When encountering obstacles during the production process, such as machine problems or staff turnover, repair the machines in time and replace the missing staff in time.
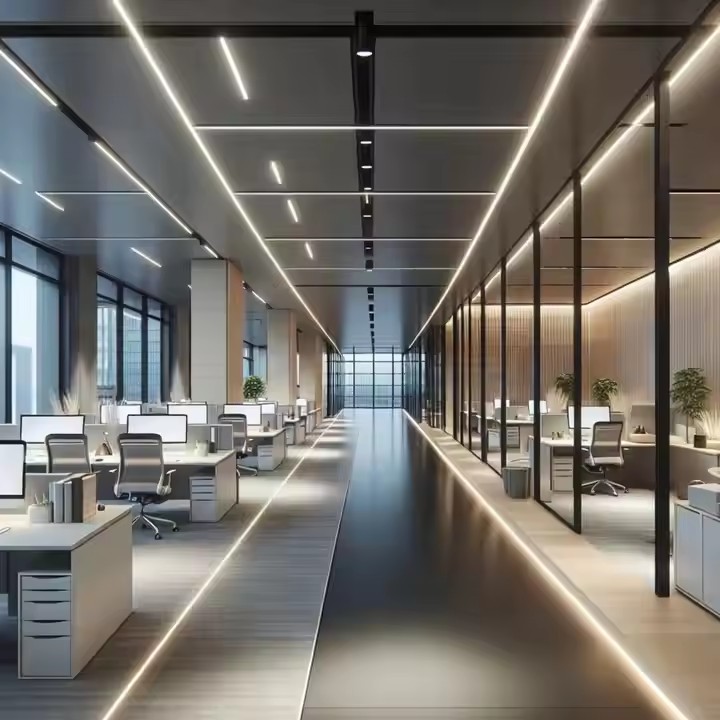
II. Raw Material Management
Procurement Management
According to the production plan and inventory situation, formulate a reasonable raw material procurement plan. For door and window production, raw materials mainly include aluminum alloy profiles, glass, hardware fittings, etc. It is necessary to ensure that the quality of the purchased raw materials meets the requirements and the price is reasonable.
Select high-quality suppliers and establish long-term and stable cooperative relationships. Conduct regular evaluations of suppliers, including aspects such as product quality, delivery period, and price. For example, conduct a quarterly assessment of suppliers.
Inventory Management
Set up a special raw material warehouse and classify and store the raw materials for easy management and access. For example, place different models of aluminum alloy profiles in different shelf areas.
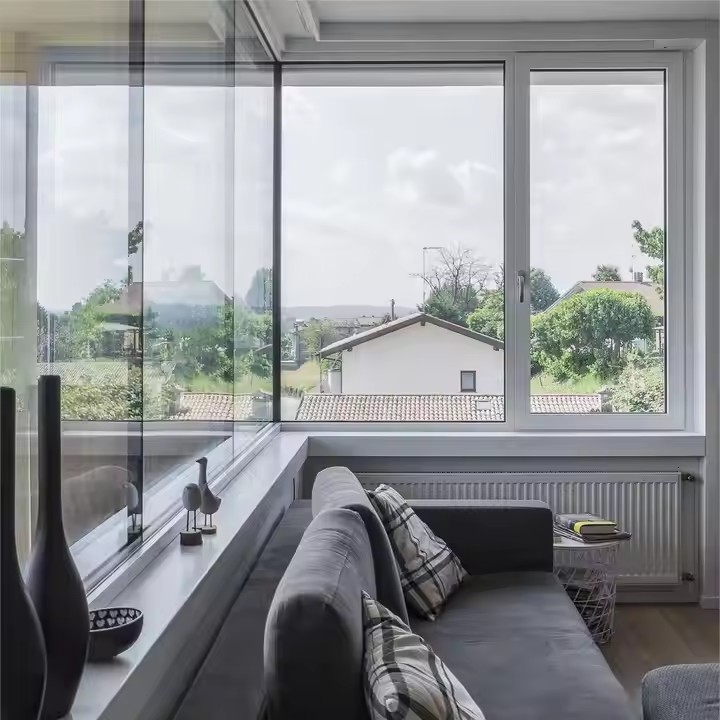
Establish an inventory counting system and count the raw material inventory regularly to ensure that the accounts match the actual situation. At the same time, reasonably control the inventory level to avoid overstocking occupying funds and prevent raw material shortages from affecting production.
III. Quality Management
Quality Standard Formulation
Based on relevant national standards and industry norms, combined with the product positioning of the enterprise itself, formulate detailed quality standards for doors and windows. Including specific indicators in aspects such as the dimensional accuracy, strength, sealing performance, and surface quality of doors and windows.
Refine the quality standards to each production process so that employees clearly know the quality requirements of each link. For example, in the cutting process, it is stipulated that the cutting length error of aluminum alloy profiles must be controlled within ±1mm.
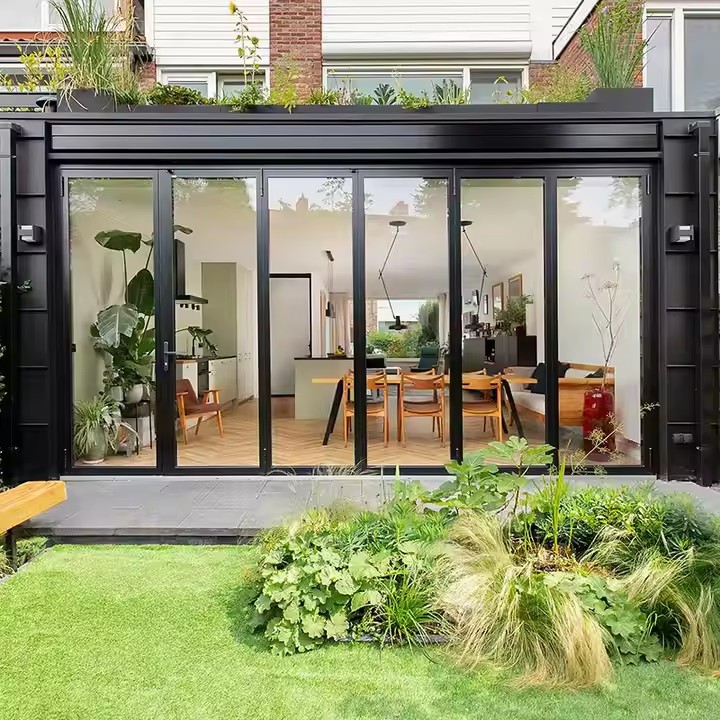
Quality Control Measures
During the production process, set up multiple quality inspection checkpoints. Such as raw material inspection, semi-finished product inspection, and finished product factory inspection. For the unqualified products detected, mark, isolate, and record them well.
Adopt quality management tools such as statistical process control to collect and analyze the quality data in the production process, and take corrective measures in time when quality fluctuations are found.
IV. Equipment Management
Equipment Maintenance
Establish an equipment ledger to record the basic information of the equipment, maintenance history, etc. Formulate a detailed equipment maintenance plan, including different levels of maintenance content such as daily maintenance, first-level maintenance, and second-level maintenance.
Maintain the equipment regularly. For example, conduct a weekly cleaning, lubrication and other daily maintenance on the equipment, a more comprehensive first-level maintenance once a month, and a second-level maintenance once every six months or a year. At the same time, manage the inventory of easily damaged parts of the equipment in advance to ensure that they can be replaced in time.
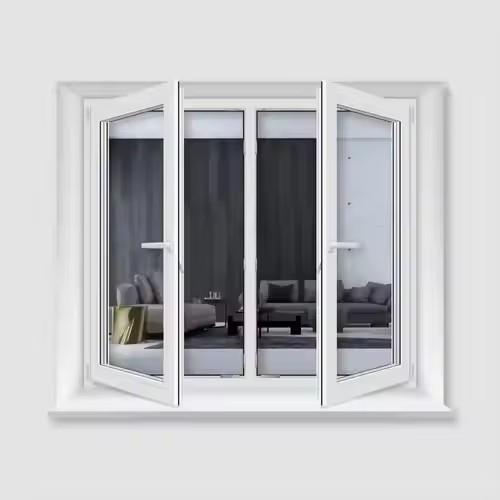
Equipment Renewal and Transformation
Pay attention to the new technologies and new trends of equipment in the industry, and update and transform the equipment in a timely manner according to the development strategy of the enterprise and the actual production needs. For example, when new automatic cutting equipment can greatly improve production efficiency and cutting accuracy, consider introducing new equipment.
V. Personnel Management
Personnel Training and Skill Improvement
When new employees join the company, conduct comprehensive pre-job training, including training in aspects such as safety production knowledge, operating procedures, and quality standards. For old employees, organize regular skill improvement training, such as inviting industry experts to give training lectures on new technologies and new processes.
Establish employee skill files to record employees’ training experiences and skill levels, providing a basis for employees’ job promotion and performance evaluation.
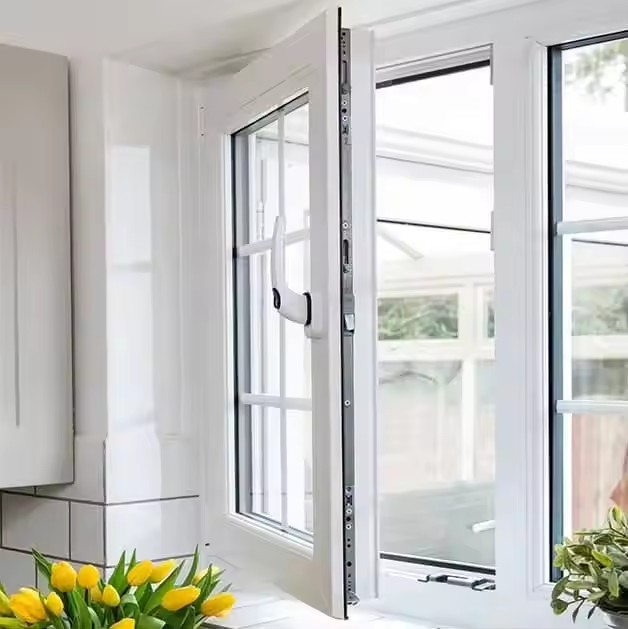
Performance Appraisal and Incentive Mechanism
Formulate a reasonable performance appraisal system and appraise employees from multiple dimensions such as production efficiency, product quality, and work attitude. For example, use the number of qualified products produced by employees and the quality pass rate as appraisal indicators.
According to the performance appraisal results, implement corresponding incentive measures, such as bonuses, honor certificates, promotion opportunities, etc., to fully mobilize the enthusiasm of employees.