- Wind Load Calculation: The Scientific Basis for Wind Resistance
Accurate load parameters are the prerequisite for wind-resistance design, requiring quantified standards based on the building environment, installation height, and door opening method.
The core calculation reference for wind load is the “Basic Wind Pressure” index specified in the Load Code for Building Structures, which is determined by the maximum wind speed occurring once every 50 years in the area (e.g., coastal areas typically ≥0.6kN/㎡, and typhoon-prone areas may exceed 1.0kN/㎡). Additionally, the “shape coefficient” of folding doors must be specially considered — when the doors are fully open, the wind-facing area sharply increases, with shape coefficients between 1.3 and 1.5. Alternating positive and negative wind pressures (such as when gusts create negative pressure indoors) must be calculated under the “most unfavorable combination,” i.e., considering the combined effect of both positive and negative pressures.
For high-rise buildings, the wind pressure height variation coefficient must be factored in: wind pressure at 10 meters above ground can differ by over 30% compared to 30 meters. Therefore, load values must be adjusted according to installation height. Also, the “dynamic wind pressure response” of folding doors should not be overlooked — pulse loads from gusts may induce resonance in the door panels. A dynamic amplification factor of 1.2 to 1.5 must be applied in calculations to prevent fatigue damage under high-frequency wind pressures.
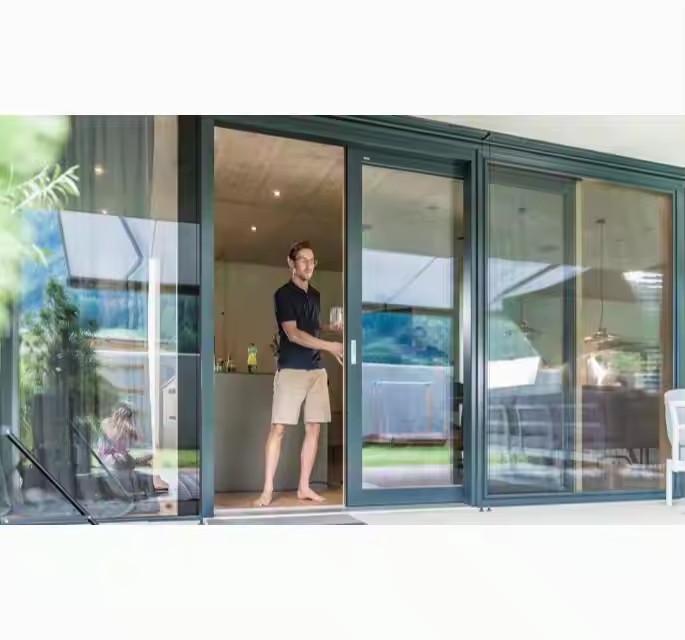
- Structural System Design: The Wind-Resistant Framework from Frame to Track
The essence of wind resistance in folding doors lies in the structure’s deformation resistance, achieved through frame rigidity, force transmission pathways, and track constraints, forming an integrated load-bearing system.
Optimizing the cross-section of frame profiles is fundamental to wind resistance. Standard folding doors use 6063-T5 aluminum profiles, but inertia must be enhanced through sectional design. The main frame is recommended to adopt a multi-chamber structure with ≥3 chambers, wall thickness ≥1.4mm (≥1.8mm in coastal areas), and cross-sectional height ≥120mm. Reinforcement ribs can be added inside the profile, and areas with concentrated forces (like hinge joints and track fixing points) should feature locally thickened designs to keep deflection under wind pressure within L/300 (where L is the door span). For ultra-wide door openings (single panel width ≥1.2m), steel-aluminum composite profiles can be used — galvanized steel liners (≥2.0mm thick) embedded inside the aluminum profile leverage steel’s high elastic modulus (about three times that of aluminum) to enhance overall stiffness.
The force transmission pathway design determines wind resistance efficiency. Wind pressure loads on folding doors should be transferred sequentially from door panel → hinge → main frame → building structure, avoiding single-point stress. Hinges, as key transmission nodes, must be made of 304 stainless steel, with load capacity ≥500N each. The number of hinges per panel should be calculated based on the load (for panels ≤80kg, at least 2 hinges each at the top and bottom). Hinges must be connected to profiles using M6 stainless steel bolts (not self-tapping screws), embedded ≥20mm deep into the profile and secured with locknuts to prevent loosening from wind-induced vibrations.
The constraint capacity of the track system directly affects wind-resistance stability. The upper track, bearing the primary wind load, should use a U-shaped deep groove design with a groove depth of ≥35mm to prevent derailing under wind pressure. The track cross-section should be a closed structure, with reinforcement flanges at the bottom (≥50mm wide), fixed to the building with expansion bolts at intervals ≤600mm, and each fixing point must bear ≥1.5kN of tension. The lower track should include guide wheels or limit blocks to restrict lateral displacement of the panels, but excessive constraints must be avoided to ensure smooth operation. An “elastic limiting design” is recommended, with a 1-2mm gap between limit blocks and door panels, allowing slight deformation while providing lateral support during strong winds.
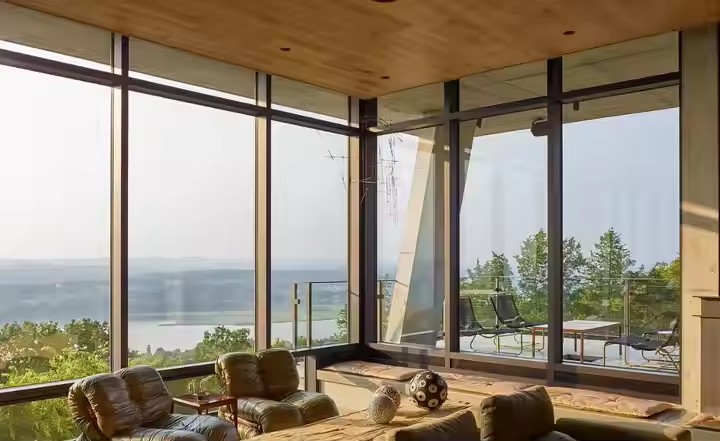
- Material Matching and Joint Sealing: Dual Protection for Wind Resistance and Sealing
Material performance and joint treatment not only affect structural stability but also prevent sealing failures and secondary damage under wind pressure.
For glass selection, both strength and safety must be ensured. Insulated glass should be tempered (≥5mm thick), with a spacer thickness of ≥12A to buffer wind pressure impact via the air gap. For single glass pieces ≥1.5㎡, laminated tempered glass (with PVB interlayer ≥0.76mm thick) should be used to maintain integrity even if shattered, preventing glass fragments from falling. Glass must be fixed to the profile using structural adhesive (not regular sealant), with a joint width ≥7mm and depth ≥5mm, ensuring wind pressure is transferred via the adhesive to the frame while avoiding stress concentration from rigid connections.
For the sealing system, wind resistance must prevent air and water leaks under pressure. Ordinary seals may bulge or flip under strong winds; therefore, a composite sealing structure should be adopted: the primary seal made of EPDM rubber strips, with a “double-lip” or “multi-lip” cross-section that presses tightly against the profile under wind pressure. An auxiliary seal with brush strips can be added at overlapping door joints to fill any gaps left by the rubber seals. In extremely high wind pressure regions, embedded seals should be used at profile junctions — inserting the rubber strip ≥8mm deep into the profile groove and securing with steel clips to prevent stripping by wind pressure.
Joint waterproofing and wind resistance coordination is also essential. The connection between the door frame and wall is a common leakage point under pressure; a stepped waterproof structure is recommended: first fill the gap with PE foam rods (diameter ≥1.5 times the gap width), then inject silicone weatherproof sealant (with movement capability ≥±25%), and finally cover with an aluminum alloy cap to block rainwater. The lower track’s connection to the ground should include a waterstop barrier (≥50mm high), integrated with the track to prevent wind-driven rainwater from seeping indoors via bottom gaps.